A380 Service 80000 Shots Mold Die Casting H13 Steel For Auto
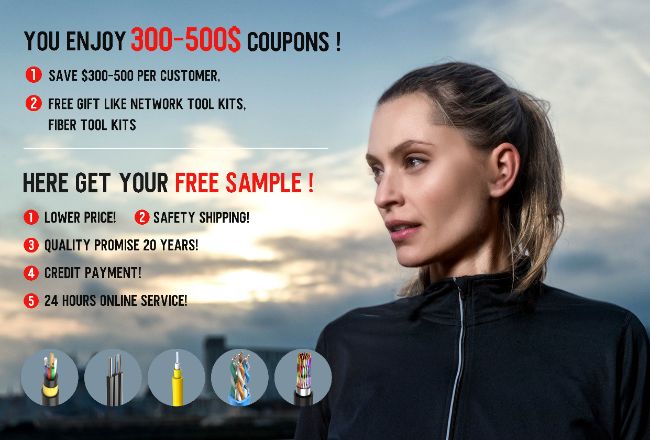
Contact me for free samples and coupons.
Whatsapp:0086 18588475571
Wechat: 0086 18588475571
Skype: sales10@aixton.com
If you have any concern, we provide 24-hour online help.
xMold Steel | P20 , H13 | Raw Material | Aluminum , Zinc , Magnesium |
---|---|---|---|
Mold Life | 50000 To 80000 Shots | Die Temperature | 288 |
Casting Temperature | 660 | Cast Machine | From 280 Ton To 1250 TON |
High Light | A380 Service Mold Die Casting,80000 Shots Mold Die Casting,H13 Steel Auto Die Casting |
Die Casting Supplier Die Casting Aluminum Custom OEM Aluminum Casting A380 Service
Die Casting Design
Before die casting your parts, manufacturers will consider a number of factors, such as: element thicknesses and intricacies (affects the amount of time the metal should spend in mold or molds) and complexity of cast design (affects solidification time). To customize a die casting process for unique requirements, manufacturers can adjust the die design, process heat, the material composition or how long the material spends in a mold.
Die and component material and hardness for various cast metals | |||||||
Die component | Cast metal | ||||||
Tin, lead & zinc | Aluminium & magnesium | Copper & brass | |||||
Material | Hardness | Material | Hardness | Material | Hardness | ||
Cavity inserts | P20[note 1] | 290–330 HB | H13 | 42–48 HRC | DIN 1.2367 | 38–44 HRC | |
H11 | 46–50 HRC | H11 | 42–48 HRC | H20, H21, H22 | 44–48 HRC | ||
H13 | 46–50 HRC | ||||||
Cores | H13 | 46–52 HRC | H13 | 44–48 HRC | DIN 1.2367 | 40–46 HRC | |
DIN 1.2367 | 42–48 HRC | ||||||
Core pins | H13 | 48–52 HRC | DIN 1.2367 prehard | 37–40 HRC | DIN 1.2367 prehard | 37–40 HRC | |
Sprue parts | H13 | 48–52 HRC | H13 DIN 1.2367 |
46–48 HRC 44–46 HRC |
DIN 1.2367 | 42–46 HRC | |
Nozzle | 420 | 40–44 HRC | H13 | 42–48 HRC | DIN 1.2367 H13 |
40–44 HRC 42–48 HRC |
|
Ejector pins | H13[note 2] | 46–50 HRC | H13[note 2] | 46–50 HRC | H13[note 2] | 46–50 HRC | |
Plunger shot sleeve | H13[note 2] | 46–50 HRC | H13[note 2] DIN 1.2367[note 2] |
42–48 HRC 42–48 HRC |
DIN 1.2367[note 2] H13[note 2] |
42–46 HRC 42–46 HRC |
|
Holder block | 4140 prehard | ~300 HB | 4140 prehard | ~300 HB | 4140 prehard | ~300 HB |
HPDC Mold Advantages
· Net shape part configuration is achievable
· High dimensional accuracy is achievable
· Fast production
· Thinner walls are achievable when compared to investment and sand castings
· Wide range of possible shapes
· External threads can be casted
· Steel inserts can be over-molded
· Holes can be cored to internal tap drill size
Typical die temperatures and life for various cast materials | ||||
Zinc | Aluminium | Magnesium | Brass (leaded yellow) | |
Maximum die life [number of cycles] | 1,000,000 | 100,000 | 100,000 | 10,000 |
Die temperature [C° (F°)] | 218 (425) | 288 (550) | 260 (500) | 500 (950) |
Casting temperature [C° (F°)] | 400 (760) | 660 (1220) | 760 (1400) | 1090 (2000) |